The Ultimate Guide to Product Packaging Maker Fixing: Keep Your Workflow Running Smoothly
Comprehending the ins and outs of packaging equipment repair is vital for preserving optimal efficiency and lessening disruptions. Normal maintenance not only expands the life of these devices but additionally addresses typical concerns that can hamper productivity.
Relevance of Routine Maintenance
Routine maintenance of product packaging devices is critical for making sure optimal efficiency and longevity. By applying a structured upkeep schedule, drivers can identify prospective issues prior to they escalate into substantial problems. This aggressive approach not just minimizes downtime however additionally prolongs the life-span of the equipment, eventually leading to minimized functional costs.
Routine examinations enable for the analysis of crucial elements such as seals, belts, and sensing units. Attending to damage promptly stops unanticipated failures that could interrupt manufacturing and bring about costly repair work. Furthermore, regular upkeep helps guarantee compliance with market criteria and laws, fostering a safe working atmosphere.
Additionally, upkeep tasks such as calibration, lubrication, and cleaning dramatically improve machine efficiency. Enhanced efficiency converts to regular item quality, which is vital for maintaining customer complete satisfaction and brand credibility. A well-kept packaging device operates at optimal rates and lowers product waste, adding to general efficiency.
Typical Packaging Machine Issues
Product packaging equipments, like any kind of complicated machinery, can experience a variety of usual concerns that may hinder their performance and performance - packaging machine repair. One common issue is inconsistent securing, which can cause product spoilage and wastefulness if bundles are not correctly sealed. This frequently results from misaligned parts or worn securing aspects
One more frequent problem is mechanical jams, which can happen due to international objects, used parts, or improper placement. Jams can trigger hold-ups in production and increase downtime, inevitably impacting total efficiency. Additionally, digital malfunctions, such as failure in sensing units or control systems, can interrupt operations and lead to unreliable measurements or irregular device actions.
Additionally, concerns with product feed can additionally occur, where things may not be provided to the product packaging area continually, causing disturbances. Wear and tear on belts and rollers can lead to suboptimal efficiency, calling for immediate interest to protect against further damages.
Recognizing these common problems is essential for maintaining the stability of product packaging procedures, ensuring that machinery runs smoothly and successfully, which subsequently helps in meeting production targets and preserving item top quality.
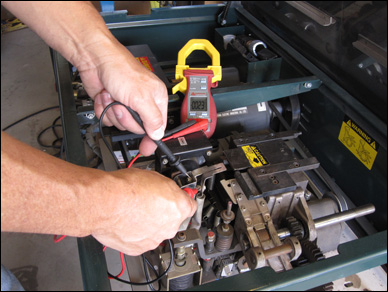
Troubleshooting Strategies
Efficient troubleshooting strategies are necessary for quickly addressing concerns that occur with product packaging makers. A systematic strategy is crucial for identifying the origin cause of breakdowns and minimizing downtime. Begin by collecting information concerning the symptoms observed; this might include uncommon noises, operational hold-ups, or error codes presented on the device's user interface.
Following, describe the device's guidebook for troubleshooting standards details to the design in inquiry. This source can provide beneficial understandings right into usual concerns and suggested analysis steps. Make use of aesthetic assessments to check for loosened links, worn belts, or misaligned components, as these physical variables commonly add to functional failures.
Carry out a procedure of removal by screening specific device features. For instance, if a seal is not developing correctly, assess the sealing device and temperature level settings to identify if they meet functional specs. Record each step taken and the outcomes observed, as this can help in future fixing initiatives.
Fixing vs. Substitute Choices
When encountered with equipment malfunctions, deciding whether to repair or change a packaging maker can be a facility and crucial option. This decision hinges on several essential aspects, consisting of the age of the maker, the extent of the Full Report damage, and the predicted influence on functional efficiency.
Firstly, take into consideration the maker's age. Older equipments may require even more frequent repair services, leading to higher cumulative expenses that can go beyond the investment in a new system.
Operational downtime is one more critical factor to consider. If fixing the maker will trigger extended delays, buying a brand-new equipment that offers boosted performance and reliability may be more prudent. Take into consideration the accessibility of parts; if replacement elements are difficult to come by, it may be a lot more calculated to change the maker completely.
Inevitably, carrying out a address cost-benefit evaluation that includes both instant and long-term implications will aid in making a notified decision that go to this website aligns with your operational objectives and budgetary restraints. (packaging machine repair)
Safety Nets for Longevity

Secret safety nets consist of routine lubrication of moving components, positioning checks, and calibration of sensing units and controls. Developing a cleaning schedule to get rid of particles and contaminants from equipment can substantially minimize deterioration (packaging machine repair). Additionally, checking operational parameters such as temperature level and vibration can help identify abnormalities at an early stage
Training personnel to acknowledge indications of wear or malfunction is one more important element of precautionary maintenance. Equipping operators with the knowledge to carry out basic troubleshooting can bring about quicker resolutions and lessen operational disruptions.
Documentation of maintenance activities, including service documents and examination searchings for, cultivates responsibility and helps with informed decision-making concerning substitutes and repair services. By prioritizing preventive actions, organizations can guarantee their packaging machines run at peak performance, ultimately bring about boosted efficiency and reduced functional expenses.
Conclusion
In verdict, the reliable repair and maintenance of product packaging devices are paramount for maintaining operational performance. Routine upkeep alleviates the risk of usual issues, such as irregular sealing and mechanical jams, while organized troubleshooting methods promote timely resolution of breakdowns. Moreover, careful factor to consider of repair versus substitute choices contributes to cost-efficient administration of sources. By applying precautionary actions, businesses can improve machine longevity and make certain uninterrupted efficiency in product packaging operations.
Understanding the complexities of packaging maker fixing is crucial for maintaining optimal performance and reducing interruptions.Routine maintenance of product packaging machines is essential for guaranteeing ideal performance and durability.Packaging devices, like any type of complex machinery, can encounter a variety of common concerns that might impede their efficiency and effectiveness. If repairing the device will create long term hold-ups, spending in a new machine that offers enhanced performance and integrity may be much more prudent.In conclusion, the reliable upkeep and repair work of packaging machines are extremely important for maintaining operational efficiency.